大家好!今天让小编来大家介绍下关于冲压产品外观设计_冲压产品外观设计图的问题,以下是小编对此问题的归纳整理,让我们一起来看看吧。
文章目录列表:

一、冲压产品外观不良现象都有哪些
不良现象有以下几点
【冲切】
(1)在批量生产前应由生产人员对将要上线的产品做一个自主首件 确认OK后再交由产线品质人员确认 产线品质人员确认OK后方可批量生产(预防批量性不良)
(2):在冲切产品外形时机器压力过大亦会导致产品边缘会出现明显的压伤
(3)在冲切产品外形时 如模板表面未清洁到位、产品表面也会造成定位批量性不良 (列如压伤 、压点)
【压合】
(1)生产部人员在生产前应检查机台参数是否符合将要生产产品的参数 检查来料是否存在不良 (如皱褶、异物、表面擦花以及各种不良)在这检查机台里是否存在有异物是否清洁 避免大批量不良
(2)上述问题如没有的话 由生产部门人员先压制4~5PNL做自主检验 确认OK后再给产线品质人员检验以及各种实验 (如外观检验、性能检验)品质人员确认OK后方可批量生产
(3)在生产过程中产线品质人员应严格要求生产部人员按照作业指导书进行作业(祥情可根据公司制度以及客户要求执行)

二、硬盘录像机申请外观专利,外观设计产品的用途和设计要点应该怎么写,有没有范例啊
1.本外观设计产品的名称:硬盘录像机件;
2.本外观设计产品的用途:本产品设计为硬盘录像机,铁皮冲压加工成型;
3.本外观设计的设计要点,包括产品的整个形状;
4.最能表明设计要点的图片或者照片:指定立体图为设计要点图片;
5,仰视图为不可见,忽略仰视图。
欢迎你加入非职务发明群交流。
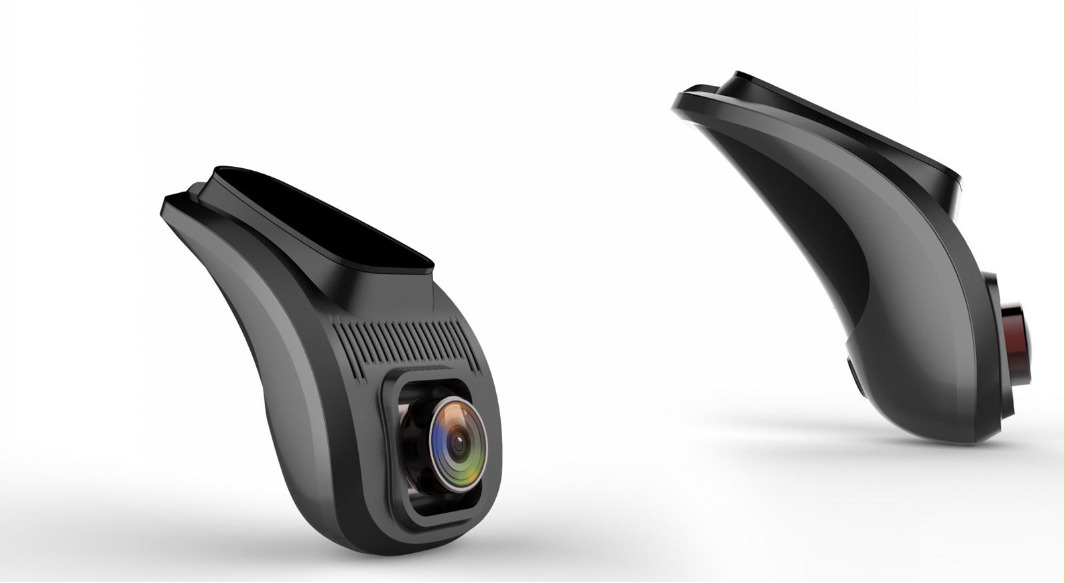
三、冲压件缺口要求标准
冲压件的缺陷及检验标准
1、目的
本标准旨在明确制造过程中对各种冲压件质量的描述、检验方法、判定标准、及对冲压件固有缺陷记录和使用标准,为制造过程质量检验提供依据。
2、范围
本标准适用于乘用车制造事业部职责范围内生产的冲压件半成品和成品。
3、术语
3.1 关键冲压件
对整车的结构、装配、生产工艺、使用性能、安全等方面有重要影响的冲压件。将这一类冲压件作为过程质量的关键环节去加以控制,列为关键冲压件。
3.2 固有缺陷
针对前期产品开发过程中,因技术、工装及设计等原因导致的冲压件存在一些工艺上无法彻底整改的缺陷。制造过程对这些缺陷进行固化和稳定。
4、冲压件质量检验标准制定原则
一个车身上的冲压件繁多,但每个冲压件的质量要求是不一样的。为了在提高整车质量的同时要充分考虑到生产技术条件和质量成本等因素,以便能够充分提高整车生产的综合效能。
因次,制定冲压件的质量检验标准需要结合生产工艺技术条件和车身的使用性能等要求,对不同类别的冲压件制定相应的质量标准。
4.1 根据冲压件在车身上功能尺寸等作用
分为:关键件和非关键件。
4.2 根据冲压件在车身上的位置不同及客户的可视程度
分为:A 、B 、C、D 四个区域。
4.3 根据冲压件上孔在车身装配及工艺要求
分为:一般孔、定位孔、装配孔。
4.4 根据冲压件上料边在车身焊接、压合等工艺要求
分为:一般料边、压合料边、焊接料边。
5、冲压件在整车上分区定义
5.1 (A 区)
车身腰线装饰条或防擦条的下边线、前翼\后翼轮罩边线等以上部位,不包括当车身前后风挡玻璃上边缘的顶盖和天窗区域。
5.2 (B 区)
车身腰线装饰条或防擦条的下边线、前翼\后翼轮罩边线等以下部位。
车身前后风挡玻璃上边缘的顶盖和天窗区域。
5.3 (C 区)
打开车门上车时能看到的部位;坐在司机或乘客座位上,关上车门后能看得见的部位;
车身发动机盖、行李盖打开后看得见区域;天窗窗框,油箱加注孔入口等其他区域。
5.4 (D 区)
除A 、B 、C 三个可视区域,车身上被内饰件等覆盖的、客户一般所不能察觉或发现的部位。
6、冲压件质量缺陷类型
冲压件质量缺陷类型一般分三类。
6.1 外观缺陷
包括:裂纹、缩颈、坑包、变形、麻点、锈蚀、材料缺陷、起皱、毛刺、拉 、压痕、划伤、圆角不顺、叠料、及其他。
6.2 功能尺寸缺陷
包括:孔偏、少边、少孔、孔径不符、多料、型面尺寸不符、其他。
6.3 返修缺陷
包括:裂纹、孔穴、固体夹杂、未溶合和未焊透、形状缺陷、变形、坑包、刨痕、抛光影、板件变薄、及其他。
7、冲压件的检验方法
7.1 外观检验方法
7.1.1 触摸检查
用干净的纱布将外覆盖件的表面擦干净。检验员需戴上纱手套沿着零件纵向紧贴零件表面触摸,这种检验方法取决于检验员的经验,必要时可用油石打磨被探知的可疑区域并加以验证,但这种方法不失为一种行之有效的快速检验方法。
7.1.2 油石打磨
用干净的纱布将外覆盖件的表面擦干净。打磨用油石 (20×13×100mm或更大)。有圆弧的地方和难以接触到的地方用相对较小的油石打磨 (例如:8×100mm 的半园形油石)油石粒度的选择取决于表面状况 (如粗糙度,镀锌等)。建议用细粒度的油石。油石打磨的方向基本上沿纵向进行,并且很好地贴合零件的表面,部分特殊的地方还可以补充横向的打磨。
7.1.3 柔性纱网的打磨
用干净的纱布将外覆盖件的表面擦干净。用柔性砂网紧贴零件表面沿纵向打磨至整个表面,任何麻点、压痕 很容易地被发现 (不建议用此方法检验瘪塘、波浪等缺陷)。
7.1.4 涂油检查
用干净的纱布将外覆盖件的表面擦干净。
用干净的刷子沿着同一个方向均匀地涂油至零件的整个外表面。
把涂完油的零件放在高强度的灯光下检查,建议把零件竖在车身位置上。用 法可很容易地发现零件上的微小的麻点、瘪塘、波纹。
7.2 尺寸检验方法
7.2.1 检具测量
利用检具、钢板尺、间隙尺等测量工具,对冲压件的孔位置、大小、型面尺寸、料边等部位进行测量。同时结合产品数模,对冲压件的尺寸进行确认。
7.2.2 三坐标、扫描测量
利用专业测量设备对冲压件孔位置、型面尺寸等进行精确测量。
8、冲压件缺陷检查标准及描述
8.1 外观缺陷检查标准及描述
8.1.1 裂纹
检查方法:目视。
对于外覆盖件任何碎裂都是不可接受的。对于内覆盖件仅细微的碎裂允许作补焊返修处理,但返修部位是顾客不易发觉的且必须满足冲压件的返修标准。
8.1.2 缩颈
检查方法:目视、剖解。
缩颈是冲压件成形过程潜在的危险破裂点,对冲压件的功能、强度、耐疲劳度有着至关重要的影响。根据缩颈的程度判定冲压件是否合格、返修、报废等。外覆盖件缩颈影响整车外观,客户是不可接受的。
8.1.3 坑包
检查方法:目视。
坑包的存在严重影响覆盖件油漆后的外观质量,是客户所不能容忍的缺陷。大面积的坑包还影响制件强度、疲劳度,无法修复。
8.1.4 变形(突起、凹陷、波浪)
检查方法:目视、油石打磨、触摸、涂油
A 类缺陷:是用户不能接收的缺陷,没有经过培训的用户也能注意到
B 类缺陷:它是在冲压件外表面上摸得着和看得见、可确定的
C 类缺陷:是需要修正的缺陷,绝大多数处于模棱两可的情况下,只有在油石打磨后才看得出。
8.1.5 麻点
检查方法:目视、油石打磨、触摸、涂油
A 类缺陷:麻点集中,超过整个面积2/3 都分布有麻点。
B 类缺陷:麻点可看到、可摸到。
C 类缺陷:打磨后可见单独分布的麻点,要求麻点间距离为300mm 或更大。
8.1.6 锈蚀
检查方法:目视、剖解。
锈蚀是冲压件长期存放或者存放不当导致生锈,对冲压件的功能、强度、耐疲劳度有着至关重要的影响。
8.1.7 材料缺陷
检查方法:目视
标准:材料强度不符合要求,轧钢板留下的痕迹、重叠、桔 、有条纹、镀锌表面疏松、镀锌层剥落。
8.1.8 起皱
检查方法:目视
外覆盖件不允许存在任何顾客容易察觉的起皱,内覆盖件不允许存在严重的起皱从而导致材料叠料。
8.1.9 毛刺
检查方法:目视
毛刺的长度要求小于板料厚度的10%。
任何影响焊接搭边贴合程度的毛刺是不可接受的。
任何容易导致人身伤害的毛刺是不可接受的。
任何影响零件定位及装配的冲孔毛刺是不可接受的。
8.1.10 拉 、压痕及划伤
检查方法:目视
外覆盖的外表面不允许存在拉 及划伤、压痕;外覆盖件的内表面不允许存在影响外表面质量的划伤、压痕。内覆盖件表面不允许存在潜在的导致零件拉裂的严重划伤、压痕。
8.1.11 圆角不顺
检查方法:目视、检具测量
圆角半径不够均匀,不够清晰光顺。外覆盖件不允许存在,内覆盖件的一些装配面、搭接面圆角不顺不仅影响制件外观,严重的还影响焊接、装配。
8.1.12 叠料
检查方法:目视
外覆盖件不允许存在叠料缺陷,内覆盖件的的不同程度的叠料缺陷 导致客户抱怨,功能类冲压件还影响制件的装配和车身强度。
8.1.13 打磨缺陷、打磨印
检查方法:目视、油石打磨
A 类缺陷:打磨穿了,在外表面上明显可见,所有顾客都立即可见。
B 类缺陷:能看到、摸到,在有争议的地方打磨后也能证明。
C 类缺陷:用油石打磨后能看出
8.2 尺寸缺陷检查标准及描述
8.2.1 孔偏、少孔
检查方法:检具测量、三坐标测量
冲压件的孔根据孔偏移的大小、孔的作用而质量标准不同。对于定位、安装孔的位置精度要求高,一般工艺孔、过孔位置精度要求低。冲压件少孔是产品设计和要求所不允许的。
8.2.2 孔径不符
检查方法:间隙尺、游标卡尺
冲压件的孔直径偏差大小,根据孔的作用而质量标准不同。对于定位、安装孔的偏差精度高低直接决定了整车的装配性能。一般工艺孔、过孔位置偏差进度要求相对低。
8.2.3 少边、多料
检查方法:检具测量、间隙尺、钢板尺、三坐标测量
冲压件少边、多料在不同类别的冲压件上影响程度大不相同。例如:焊接边少边影响焊点分布和操作,压合边少边和多料决定压合后总成质量。
8.2.4 型面尺寸不符
检查方法:检具测量、间隙尺、钢板尺、三坐标测量
冲压件型面尺寸偏差由于设计、规划等工艺水平是避免不了的,但是其偏差的大小直接决定了整车的外观配合、冲压件匹配、零部件装配等质量水平。
9、冲压件缺陷检验判定标准
以下标准,遵循“质量从严”的原则进行判定。同一问题按严重程度从严判定。
9.1 外观缺陷检验判定标准
冲压件外观缺陷检验标准
项目
描述
关键件
判定(整车区域)
裂纹
1、 封闭裂纹: 长度≥50mm
宽度≥3mm
2、 不封闭裂纹:长度≥30mm
宽度≥2mm
/
所有件下同
报废
1、 封闭裂纹:10mm≤长度<50mm
宽度<3mm
2、 不封闭裂纹:10mm≤长度<30mm
宽度<2mm
是
报废
非
返修
1、封闭裂纹: 长度<10mm
宽度<3mm
2 、不封闭裂纹:长度<10mm
宽度<2mm
/
返修
缩颈
缩颈部位材料厚度:厚度≥料厚的
80 %;缩颈部位长度≥60mm
/
报废
缩颈部位材料厚度:料厚的50%≤厚度<料厚的80%; 缩颈部位长度:30mm≤长度<60mm ;
是
报废
非
返修
缩颈部位材料厚度:厚度<料厚的
50 %缩颈部位长度:长度<30mm
/
返修
坑包
面积≥8m㎡ ;长度≥10mm ;
高度≥1.5mm
/
返修
面积<8m㎡ ;长度L<10mm ;
高度<1.5 mm
/
返修
变形
零件表面出现明显起伏;目视明显;严重影响外观及装配
/
报废
零件表面出现起伏;目视不明显;手感明显
/
返修
零件表面出现起伏;手感不明显;油石检验明显
/
合格
麻点
零件2/3 面积上能看到麻点或小凸包
/
报废
零件表面用油石磨件之前用手感觉明显的麻点或麻点群;麻点面积<2/3 零件面积;
/
返修
材料缺陷
料厚明显不符合要求;表面有明显的桔皮滑移线、镀锌层疏松;锌 脱落长度≥300 mm ;宽度≥5mm
/
报废
轻微的材料缺陷;磨件后可见的材料缺陷;
/
合格
锈蚀
锈蚀厚度≥料厚的40% ;
锈蚀面积≥全部面积的25 %;
型面比较复杂无法消除锈迹;
/
报废
锈蚀厚度:料厚的20%≤厚度<料厚的40 %;
锈蚀面积:全面积5%≤厚度<全面积25 %;
是
报废
非
返修
表面质量受锈蚀影响但可通过打磨修复;
/
返修
起皱
肉眼能看出的严重皱折、棱线错位,严重影响焊接及装配;
/
报废
棱线、弧度不够清晰光顺;
肉眼可见的皱纹、波纹、棱线错位;
是
报废
非
返修
毛刺
毛刺高度H 大于料厚的40% ;有操作危险性的粗毛刺;
/
返修
毛刺高度:料厚的20%≤高度<料厚的40 %;毛刺影响定位、装配、焊接、压合的;
一般孔
合格
定位孔装配孔
返修
一般料边
合格
压合/焊接料边
返修
毛刺高度:高度<料厚的20 %;
/
合格
拉毛压痕划伤
深度≥料厚的30%;宽度≥2mm ;长度≥5mm ;
是
报废
非
返修
料厚的 10%≤深度<料厚的 30% ;宽度<2mm ;长度<5mm
/
返修
深度<料厚的10%;
/
合格
圆角不顺
圆角半径不均匀,未达到要求;明显地不清晰、不光顺;配合间隙达2 mm 以上;
/
报废
圆角半径不均匀,不够清晰光顺;配合间隙达2 mm 以下
/
返修
叠料
板料重叠宽度:宽度≥8mm
/
报废
板料重叠宽度: 3mm≤宽度<8mm
是
报废
非
报废
板料重叠宽度:宽度<3mm
/
返修
其他
能引起严重功能障碍的缺陷
报废
对使用有明显影响的缺陷
返修
四、汽车覆盖件的钣金冲压模具设计和开模一共大概多少钱,只要四个车门的话多少钱,用于个性改装?
感谢笔者有如此想法。
本人在一汽大众下级供应商上班,对于冲压件有一定的了解。首先汽车车门的覆盖钣金属于A级外观件,大部分主机厂自行生产,很少有外发。其次,产品难度较大,没有个十多年钣金生产经验的厂家不敢尝试。
再来说说开模费用,四套车门,至少需要16套冲压模具,按照2500T多工位设备开模,每套模具均重10吨,模具费用至少在600W。(汽车模具一般3.5-5.5万元/吨)。如果没有上千的产量,建议不要轻易尝试。汽车行业的水还是挺深的。
以上就是小编对于冲压产品外观设计_冲压产品外观设计图问题和相关问题的解答了,冲压产品外观设计_冲压产品外观设计图的问题希望对你有用!
免责声明: 1、文章部分文字与图片来源网络,如有问题请及时联系我们。 2、因编辑需要,文字和图片之间亦无必然联系,仅供参考。涉及转载的所有文章、图片、音频视频文件 等资料,版权归版权所有人所有。 3、本文章内容如无意中侵犯了媒体或个人的知识产权,请联系我们立即删除,联系方式:请邮件发送至 cnc1698@l63.com